Maintenance Training and Asset Management: Creating Value in Manufacturing
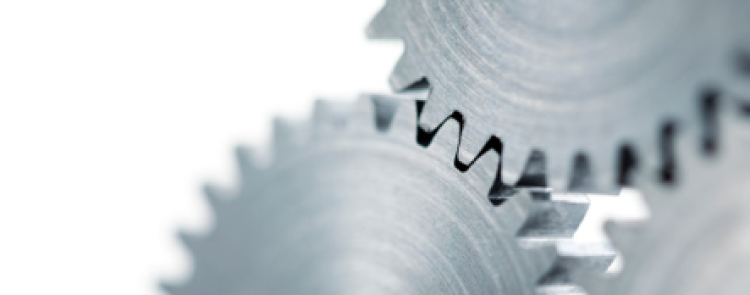
With all the efforts, strategies and objectives surrounding preventative and predictive maintenance, not one can be accomplished without a properly targeted training program. This article on http://www.uesystems.com “Education and asset management: Reliability minus training equals failure” details some of the areas maintenance managers should focus on when considering a skills development initiative for their respective departments.
Here are a few of the key takeaways, and strategies that we at Scientific Management Techniques (SMT) have built into our curriculum delivery:
- Hands-On Training – Manufacturing is a hands-on industry, and people naturally learn best by doing. SMT teaches theory that is then put into practice using over 200 training aids that replicate conditions in industry. Examples include our newly developed Process Control trainer, Pneumatic and Hydraulic trainers, and a Packaging Machine Simulator.
- Direct Application – Training isn’t effective if it isn’t relevant. Delivering training that is directly tied to an end goal or end process is key to maximizing ROI. SMT’s training is customized to each and every client utilizing a curriculum that is 100% demand-driven by industry professionals. By deploying a program such as this, you are in fact utilizing the combined manufacturing expertise of Fortune 500 clients such as Pfizer, Unilever, Medtronic, Proctor & Gamble, Reckitt Benckiser, Diageo, Wrigley, and more.
- Measurement and Continuous Improvement – “If you can’t measure it, you can’t improve it.” Commonly used, this statement speaks for itself. Developing methods of measurement is one of the most challenging, but one of most fundamentally important aspects of industry training. Utilizing a pre and post-assessment methodology enables training to be continuously developed and improved upon.
The article then describes some common pitfalls or reasons used to avoid training:
- Fear that trainees will leave
- Failure to create a learning environment
- Failure to reinforce or refresh
- Failure to identify the skills required for equipment use
Clearly, these thoughts and theories should be avoided or discarded as they are detrimental to improving workforce productivity. If done properly, training is a win-win scenario that creates a sense of worth and loyalty in your employees, while maximizing their utility to the company and improving your bottom line performance.