The Standard Timing Model – Quantifying Industrial Skills for Hiring
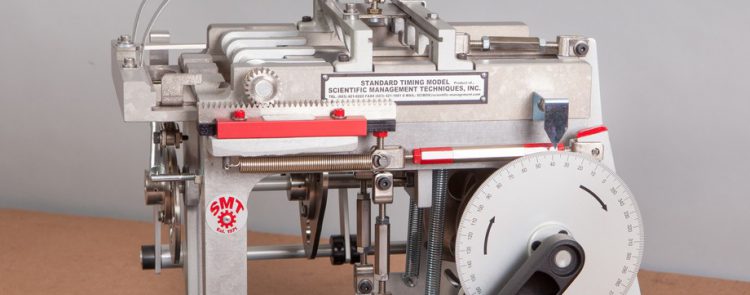
The manufacturing skills gap is becoming an ever more extensive problem as global manufacturing continues to rebound.
One of the most difficult tasks for hiring managers in the industrial space is getting a true read on the hard skill sets of job candidates. Difficulty finding qualified labor to fuel that growth threatens to negatively impact manufacturers well into the next decade.
A candidate can interview well, even post good scores on a pencil & paper test, but without physically putting their troubleshooting skills to the test, there is no real way to know what level of performance you are getting. Scientific Management Techniques, Inc. has developed a series of five, completely unique, validated Assessment Machines for exactly this purpose.
Our most widely used machine is the Standard Timing Model (STM); a mechanical assessment device used by many Fortune 500 manufacturers across the globe for over 40 years. The STM assessment protocol combines a series of standardized faults that the candidate then has to troubleshoot in order to achieve a time. This time can then be compared to others to create a ranking.
Testing Job Candidates
The STM has 3 primary applications when used in the hiring process:
- Maintenance level assessment: Identify and measure a “pre-existing” skill set for an experienced maintenance professional. Someone that will be productive immediately.
- Operator level assessment: Identify and measure a “pre-existing” skill set for an experienced/trained operator.
- Identify mechanical aptitude/instinct: in individuals you know have not been properly trained, or perhaps have never worked in a manufacturing environment. For this we administer the “operator level” assessment but have a different score expectation. Our clients use this capability when they are hiring individuals they know they will need to train. Someone with mechanical aptitude is significantly more trainable than someone with little to zero aptitude.
Testing Employees
Additionally, the STM and other Assessment Machines can help to quantify the skill sets of existing incumbent personnel. This could be done to:
- Deliver highly targeted training. This is essential to maximizing both financial and operational efficiency. The less time spent training, the less time spent away from normal job responsibilities.
- Training Post-Assessment: Gauge the effectiveness of training delivered.
- Target promotions or pay raises to those individuals with the most advanced sets of skills.
Most importantly, the ROI of SMT’s Assessment Program Exceeds 100% the first year of deployment. The assessment program stops the “bad hire”, those individuals that may interview well but you recognize quickly that he or she does not possess the skills they represented.
How many “bad hires” did you have last year? Over the last 5 years? What would the impact have been if all these hires were top performers? Turnover has hefty realized and unrealized costs. That is the impact the assessment program delivers.
SMT has over 35 validation studies and 40+ years of data proving the efficacy of the skills assessment program. It just flat out works, adding performance and profitability for any business unit that has deployed and used it according to our methodology.
There are four other skill assessment machines offered:
- Electrical Skills Test Device (ESTD)
- Programming Logic Control Test Device (PLCTD)
- Computer Numeric Control Test Device (CNC)
- Process Control Test Device (PCTD)
Identifying and measuring skills prior to hire is the single most effective means to insure a quality, highly productive hire in manufacturing.